Using Oil Analysis for Lubrication Management
There is no question that an effective oil analysis program lowers maintenance... Read more »
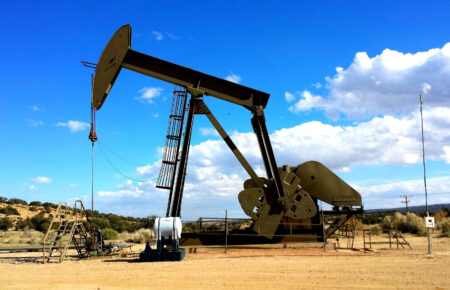
Get the most out of your time at Reliable Plant Conference by adding one of these special experiences to your registration.
Reliable Plant Conference & Exhibition will be held at the Renaissance Schaumburg Convention Center Hotel in Chicago and attendees will receive discounted room rates.
See inside the reliability event that brigs maintenance reliability professionals from all over the world! Did you see yourself in a photo or video? Download and share!
Thank you to our sponsors for making Reliable Plant 2025 possible! Your trust and contributions help us bring more maintenance and reliability professionals together.
2 articles found
There is no question that an effective oil analysis program lowers maintenance... Read more »
The primary source of lost revenue due to downtime of equipment is... Read more »
Be the first to get conference updates!
We'll never spam you. View our privacy policy.
Less $75 processing fee if written request of cancellation is received prior to 04/03/2025 12:00AM CST. No refunds processed after 04/03/2025 12:00AM CST.
Cookie | Duration | Description |
---|---|---|
cookielawinfo-checkbox-analytics | 11 months | This cookie is set by GDPR Cookie Consent plugin. The cookie is used to store the user consent for the cookies in the category "Analytics". |
cookielawinfo-checkbox-functional | 11 months | The cookie is set by GDPR cookie consent to record the user consent for the cookies in the category "Functional". |
cookielawinfo-checkbox-necessary | 11 months | This cookie is set by GDPR Cookie Consent plugin. The cookies is used to store the user consent for the cookies in the category "Necessary". |
cookielawinfo-checkbox-others | 11 months | This cookie is set by GDPR Cookie Consent plugin. The cookie is used to store the user consent for the cookies in the category "Other. |
cookielawinfo-checkbox-performance | 11 months | This cookie is set by GDPR Cookie Consent plugin. The cookie is used to store the user consent for the cookies in the category "Performance". |
viewed_cookie_policy | 11 months | The cookie is set by the GDPR Cookie Consent plugin and is used to store whether or not user has consented to the use of cookies. It does not store any personal data. |