I’ll admit it. I am an input junky. Any time I am looking to make a purchase, I research the potential products or services exhaustively. User reviews, performance tests and data, specifications, consumer reports, you name it I want to read it. While the casual observer might suggest that I am simply a gluten for punishment, the truth is that I have learned over the years that making an uniformed decision gives one a low likelihood of making a good decision. The difference between a good purchasing decision and a poor one lies in just one thing; value. A good decision means that there is value gained as a result of the purchase.
To call today’s steel industry challenging might be the understatement of the year. Raw material prices trending up, steel prices flat at best, and demand has no where near returned to pre-recession levels. When capacity utilization is low in an asset intensive environment, the high fixed cost makes it difficult to turn a profit. We must make good decisions in how we operate and maintain our plants. Good decisions that add value to the business. This means we need input, and lots of it. Managing a business making decisions based on gut feelings just doesn’t cut it these days.
The business of managing maintenance is no different then any other business. Repair and Maintenance (R&M) operating and capital dollars are allocated, and in return the company expects value to be delivered in the form of reliable assets. Maintenance Key Performance Indicators (KPI’s) provide input to decisions made in the quest to meet this lofty objective.
Ground Rules
KPI’s can be very specific to an individual’s activity, or broad enough to measure an entire plants performance. They can be leading or lagging, simple counts or complex calculations. They should follow a few simple ground rules, however, to ensure they provide quality input.
- Metrics should be easily connected to the business value that strong performance will deliver (how does knowing what color boots the electricians wear help me?).
- Metrics should be aligned with the current state of the organization (% proactive work will be very misleading if we are only capturing 50% or our work on work orders).
- Metrics should be automated (manual counts are riddled with errors and often get neglected).
- Metrics should follow a process or practice (activities should not be added to a process solely to make the KPI measurable).
- Metrics should have reasonable, defined and understood targets (be careful of the law of diminishing returns).
- Metrics should be monitored and responsible parties held accountable for their results (building them into performance objectives and incentives has proven very successful).
Maintenance Key Performance Indicators Alignment to Business Process
A well defined business process needs to be executed well in order to deliver the desired result. In other words, the engine needs to be running on all 8 cylinders to make the horsepower needed to win the race.
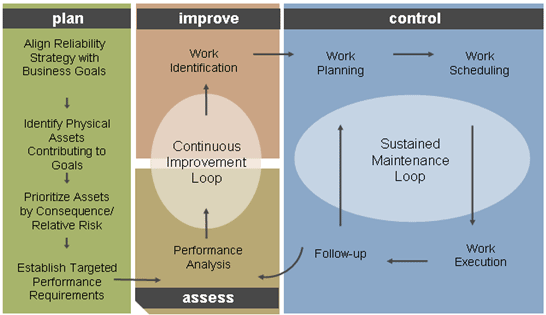
The figure above illustrates the ArcelorMittal USA Maintenance Business Process. Each component contains specific activities and practices essential to delivering business value to the stakeholders. Each component’s activities are monitored with a set of standardized maintenance key performance indicatorsto provide managers with the input needed to make informed decisions, and enact corrections and improvements as appropriate.
Plan
The “Plan” component of the Business Process sets the stage for all other activities. It involves understanding the business objectives, identifying physical assets that support those objectives, analyzing the consequences and risk those assets represent, and establishing performance requirements needed to reach the business requirements. While these activities primarily lead to the development of targets for metrics used to monitor downstream activities, there are some examples of maintenance key performance indicatorsused to monitor this component of the Business Process.
- % of assets with Asset Prioritization Analysis completed
- Maintenance Budget as a % of RAV
Improve
The “Improve” component of the business process is all about Work Identification. Simply stated, Work Identification is the development of a technically valid maintenance program for the assets identified on the “Plan” component of the business process. This is accomplished by using methodologies such as Reliability Centered Maintenance, Maintenance Task Analysis and Root Cause Analysis to identify the tasks that will most cost effectively mitigate the consequences of failure. Some examples of KPI’s used to monitor progress include:
- # of failure modes identified
- % of maintenance action plans implemented
- # of condition inspections implemented
Control
The “Control” component of the Business Process is about effectively and efficiently executing the maintenance program developed and implemented in the “Improve” component. Maintenance tasks are planned, scheduled, executed, and follow-up activity performed to improve maintenance plans. This is called the “Sustained Maintenance Loop”. Metrics monitor many aspects of this component to understand the quality of maintenance planning, effectiveness of scheduling, and efficiency of execution. Some examples include:
- % of backlog ready to work
- Planned vs. actual man-hours
- % of scheduled outage work orders completed
- % PM compliance
Assess
The “Assess” component of the Business Process is where performance is compared to targets to understand where further improvement is needed. Mainly lagging KPI’s are reviewed in this component. These KPIs vary based on the type of unit. For example MTFB is valuable for continuous processes where each line stop results in significant yield loss. Batch processes tend to look more at delay rates or production metrics. Some examples include:
- Working Ratio
- Heats per day
- Budget vs. Actual R&M Spend
- Prime Yield
Calculation andReporting
KPI’s are automatically calculated and available in real time on dashboards in the Reliability Software. Inputs to the calculations come from the Reliability System, the CMMS, Operating data, and financial reporting.
The standardized list of KPI’s are deployed at the corporate level, plant level, and the individual business level within each plant. They can be accessed and navigated to for real time data at any time.
Dashboards are also created to meet the needs of specific roles in the organization such as Plant managers, Maintenance Managers, or Planners.
KPI data is also compiled in reports monthly for review meetings and distribution to upper management.
Maintenance Key Performance Indicators provide valuable input to make decisions within the Maintenance Business Process. Informed decisions ensure business value that moves the organization towards meeting the objectives of the stakeholders. It is essential that KPI’s are aligned with the organizations Maintenance Business Process, and that they are defined, understood, and communicated across the company.
By Darrin Clark, ArcelorMittal USA
This article was previously published in the Reliable Plant 2013 Conference Proceedings.